1 min read
Design for Minimal Post Processing: Save Time and Costs with Smart Design
Nick Erickson : Sep 10, 2024 12:47:27 PM
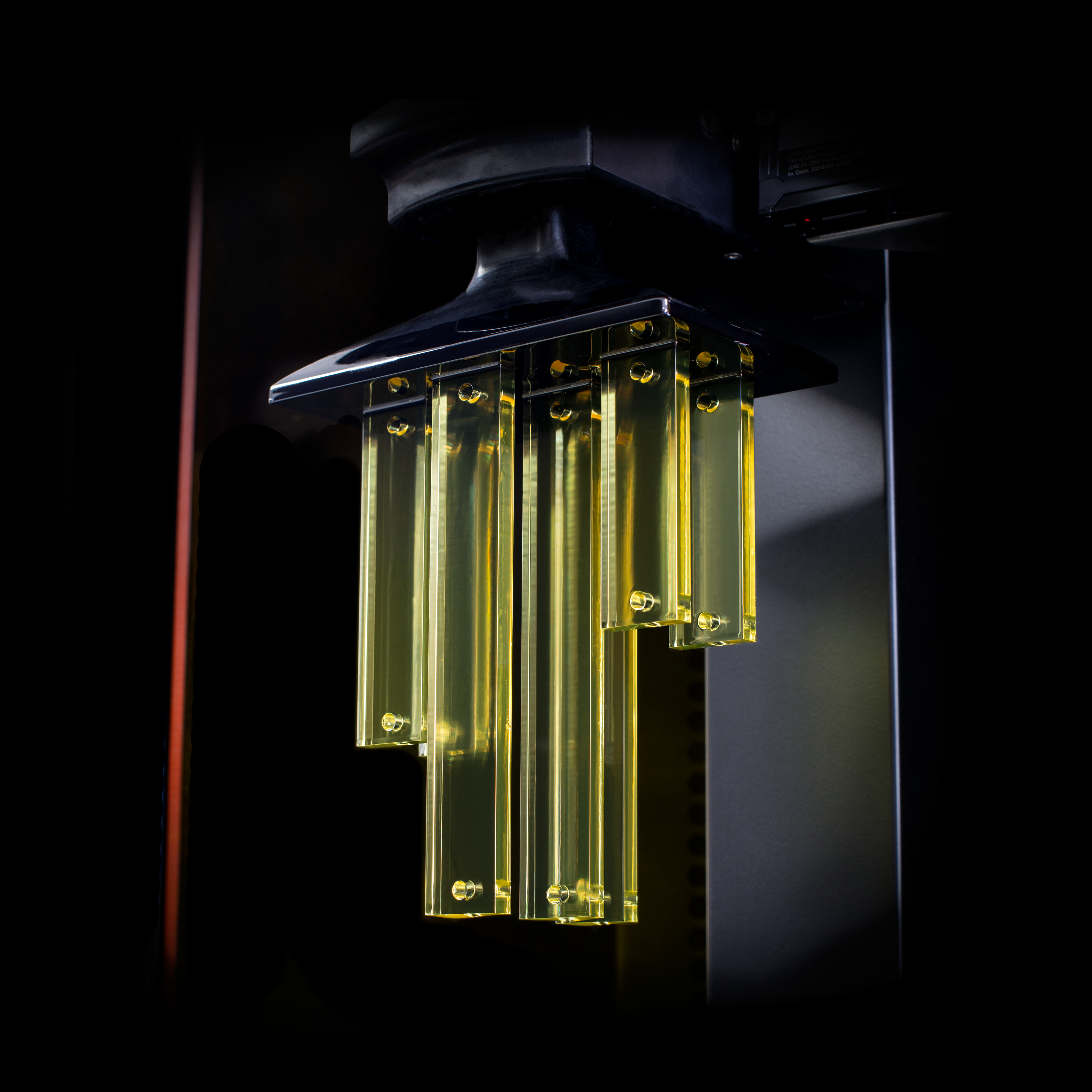
R&D engineers and product designers are always balancing time, cost, and quality. Post-processing can be a drain on all three, so designing to minimize post-processing makes a lot of sense. The key lies in foresight and strategic planning during the design phase to ensure that the final product emerges as close to perfect as possible right out of the printer.
Here’s how you can build it into your workflow.
Integrated Features: By designing in functional elements like threads or snap-fits, you can bypass the need for machining or secondary operations after printing. This is especially valuable during the prototyping phase. For instance, if you’re developing a medical device connector, embedding threaded inserts right into the part design can eliminate manual intervention, reducing lead times and potential human error.
For R&D teams, this can mean quicker iterations and a more streamlined path to testing. Additionally, incorporating features such as living hinges or interlocking joints can further reduce the need for assembly and secondary processing, providing a seamless and cohesive prototype that is ready for immediate evaluation and testing.
Reduce Supports in Critical Areas: No product designer wants to mar the appearance or functionality of a part with post-processing. By placing support structures in non-visible or non-functional areas, you avoid having to smooth or clean these critical sections after printing. Think of a shoe midsole where internal supports are hidden—your external surfaces remain flawless, which is key in consumer product development where aesthetics are just as important as function.
Another approach is to design parts with self-supporting angles or built-in scaffolding that can be easily removed without affecting the critical surfaces. This ensures that the final product retains its intended look and functionality, minimizing the need for extensive post-processing work.
Designing for minimal post-processing reduces time, manual labor, and the chance of introducing flaws into your prototype or final product, giving you a cleaner, more efficient development process. This not only accelerates the time-to-market but also enhances the overall quality and reliability of your designs, enabling you to focus more on innovation and less on rework. By integrating these strategies into your workflow, you can achieve a harmonious balance between time, cost, and quality, driving successful outcomes in your product development journey.
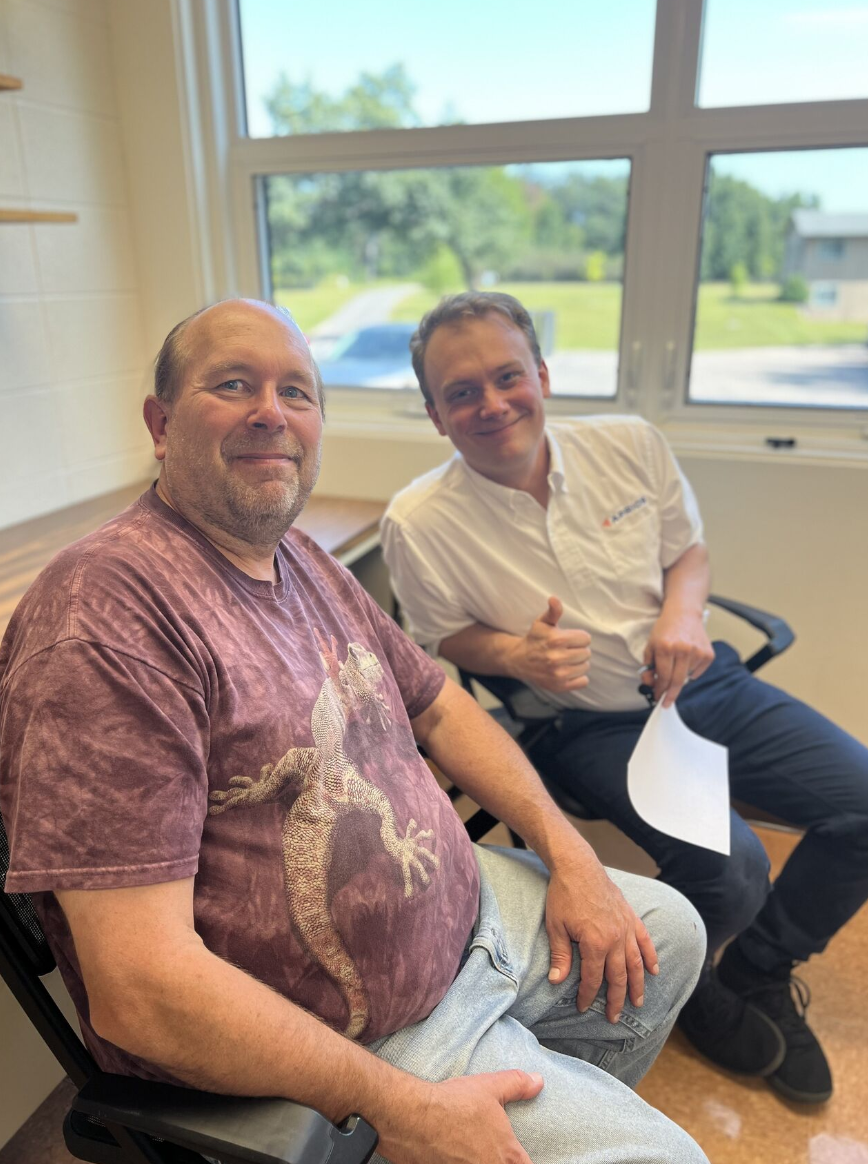
Aprios: Supporting Long-Term Ecological Research at Cedar Creek
Cedar Creek Ecosystem Science Reserve: How Aprios Supports Long-Term Ecological Research
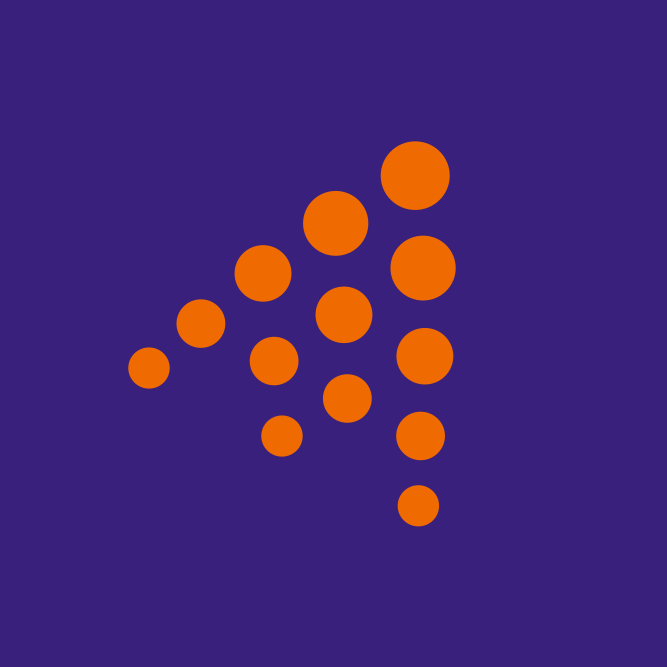
Utilizing Overhangs and Underhangs in Medical Device Design
Harnessing the Power of Overhangs and Underhangs in Medical Device Innovation Introduction