DESIGN FOR MANUFACTURING
We help your
mental sketches
take solid form.
Optimize your product for efficient manufacturing and streamlined assembly—
reducing costs and accelerating production.
Better Designs Lead to Better Products
DFM ensures that your designs are optimized for efficient, cost-effective production and assembly. At Aprios, we focus on creating parts and assemblies that streamline the manufacturing process, reduce waste, and enhance quality. By carefully selecting materials and designing parts that align with the capabilities of both injection molding and 3D printing, we help you minimize production costs and lead times, delivering high-quality results that meet your needs and exceed your expectations.
DFM in Plastic Injection Molding: Practical Design Tips for Better Parts
A quick-start guide for engineers designing smarter, more manufacturable plastic parts.
WHAT'S INSIDE:
- Draft angles, wall thickness, and parting line best practices
- How to avoid common pitfalls like sink, warping, and knit lines
- Tooling design insights: gating, venting, and mold flow
- Rib, boss, and corner radius guidelines
- How mold flow analysis helps you get it right the first time
What DFM Can Do for You
By incorporating DFM principles, we help you create designs that are easier and cheaper to manufacture, improving the quality and performance of your products. Let us work together to optimize your designs for manufacturability, ensuring your business benefits from reduced costs, enhanced durability, and quicker production times.
Simplifying Part Design and Ensuring Consistency
Simplifying part design reduces mold complexity and costs, while maintaining uniform wall thickness helps prevent issues like warping and incomplete filling. By opting for straightforward designs over intricate ones, production becomes more efficient. Our DFM design approach provides cost-effective solutions.
-
Managing Complex Shapes
- Simplifying the geometry of your parts reduces the complexity of the mold, making manufacturing easier and more cost-effective. For instance, opting for straightforward geometries over intricate undercuts allows for simpler, cheaper mold designs.
-
Uniform Wall Thickness
- Maintaining consistent wall thickness helps avoid issues like warping, sinking, or incomplete filling. For example, ensuring uniform walls in electronic device housings promotes proper cooling and prevents uneven shrinkage.
Avoiding and Resolving Failure Points
Designs are refined to avoid potential failure points by using fillets instead of sharp corners, which distributes stress evenly. This practice enhances durability in both injection molding and additive manufacturing applications.
-
Avoiding Sharp Corners
- Sharp corners can create stress concentrations and potential failure points. Instead, use fillets (rounded corners) to distribute stress more evenly and improve the flow of molten plastic.
-
Eliminating Tooling Pitfalls
- Designing parts to avoid undercuts (a feature of a molded part that prevents the part from being ejected from the mold without additional mechanisms or actions) that require side actions or lifters in the mold can significantly reduce costs and complexity. For instance, designing snap-fit features without additional mold movements streamlines production.
Enhancing Part Strength and Ease of Assembly
Rather than increasing wall thickness, strategically placed ribs add strength and rigidity. Bosses are integrated for fastening, ensuring stability and durability across both injection molding and additive manufacturing processes.
-
Using Ribs to Increase Part Strength
- Instead of increasing wall thickness, add strength and rigidity with strategically placed ribs. For example, a thin-walled plastic cover can achieve enhanced structural integrity through well-placed ribs.
-
Bosses for Assembly
- Integrate bosses (cylindrical protrusions) for screws or fasteners in areas needing assembly, ensuring they are supported by adjacent walls or ribs to distribute stress and maintain durability.
Optimized Material Selection and Usage
Choosing the appropriate materials is crucial. Our material recommendations are selected to meet performance requirements, such as high-flow thermoplastics for injection molding or specialized resins for additive manufacturing. This approach ensures proper filling, reduces cycle and print times, and enhances efficiency.
-
Avoiding Sharp Corners
- Selecting materials that are compatible with injection molding and meet the performance requirements of your parts is crucial. Using a high-flow thermoplastic for thin-walled parts ensures proper filling and reduces cycle times, enhancing efficiency.
Learn About DFM
with Ray Schenk
Watch our Senior Engineer, Ray Schenk, discuss the value of Design for Manufacturing (DFM) in this insightful video. Ray explains how DFM principles enhance manufacturability, reduce costs, and improve product quality, providing our customers with efficient and effective production solutions. Discover how integrating DFM into your design process can transform your manufacturing outcomes.
Find the Right Material for Your Application
Material selection plays a critical role in manufacturability, performance, and cost. Whether you need high-temperature resistance, flexibility, chemical compatibility, or medical-grade biocompatibility, Aprios offers a comprehensive selection of thermoplastics, elastomers, and high-performance materials for injection molding and additive manufacturing.
Our thermoplastic material selection guide will help you:
- Browse materials by category, properties, and applications.
- Compare options for strength, rigidity, thermal resistance, and more.
- Understand which materials are best suited for your project’s requirements
Understanding the Boundaries of DFM
DFM is a powerful tool for enhancing manufacturability and efficiency, but it works best when integrated with comprehensive design, engineering, and quality control practices.
-
DFM Isn't a Substitute for Detailed Engineering and Product Development
While DFM optimizes designs for manufacturability, it doesn't replace the need for detailed engineering and thorough design work. It enhances the process but can't compensate for a lack of technical precision or thorough design validation.
-
DFM Isn't a One-Size-Fits-All Solution
DFM principles vary depending on the manufacturing method, materials, and product requirements. What works for injection molding may not apply to additive manufacturing, and vice versa. DFM must be tailored to each specific project to be effective.
-
DFM Isn't a Guarantee of Perfect Products
Even with optimized designs, unforeseen issues can arise during production. DFM minimizes risks and enhances manufacturability, but it doesn't eliminate the need for rigorous quality control and testing throughout the production process.
-
DFM Isn't a Replacement for Prototyping
While DFM can reduce the need for multiple design iterations, it doesn't eliminate the need for prototyping. Prototyping is still essential to test and validate the physical aspects of a design before full-scale production.
-
DFM Isn't a Quick Fix
Implementing DFM principles requires time and collaboration between design and manufacturing teams. It’s an investment in the design phase that pays off in production efficiency and cost savings, but it isn't an immediate solution for existing manufacturing issues.
-
DFM Isn't an All-Inclusive Cost Reduction Strategy
While DFM can lead to cost savings by optimizing the design for efficient production, it doesn't account for all potential cost factors. Material costs, labor, and overhead still play significant roles in the overall production cost.
-
DFM Isn't Solely About Simplification
DFM focuses on optimizing designs for manufacturing, which sometimes involves simplification, but it also includes strategic enhancements. The goal is to make the design manufacturable without compromising functionality or performance.
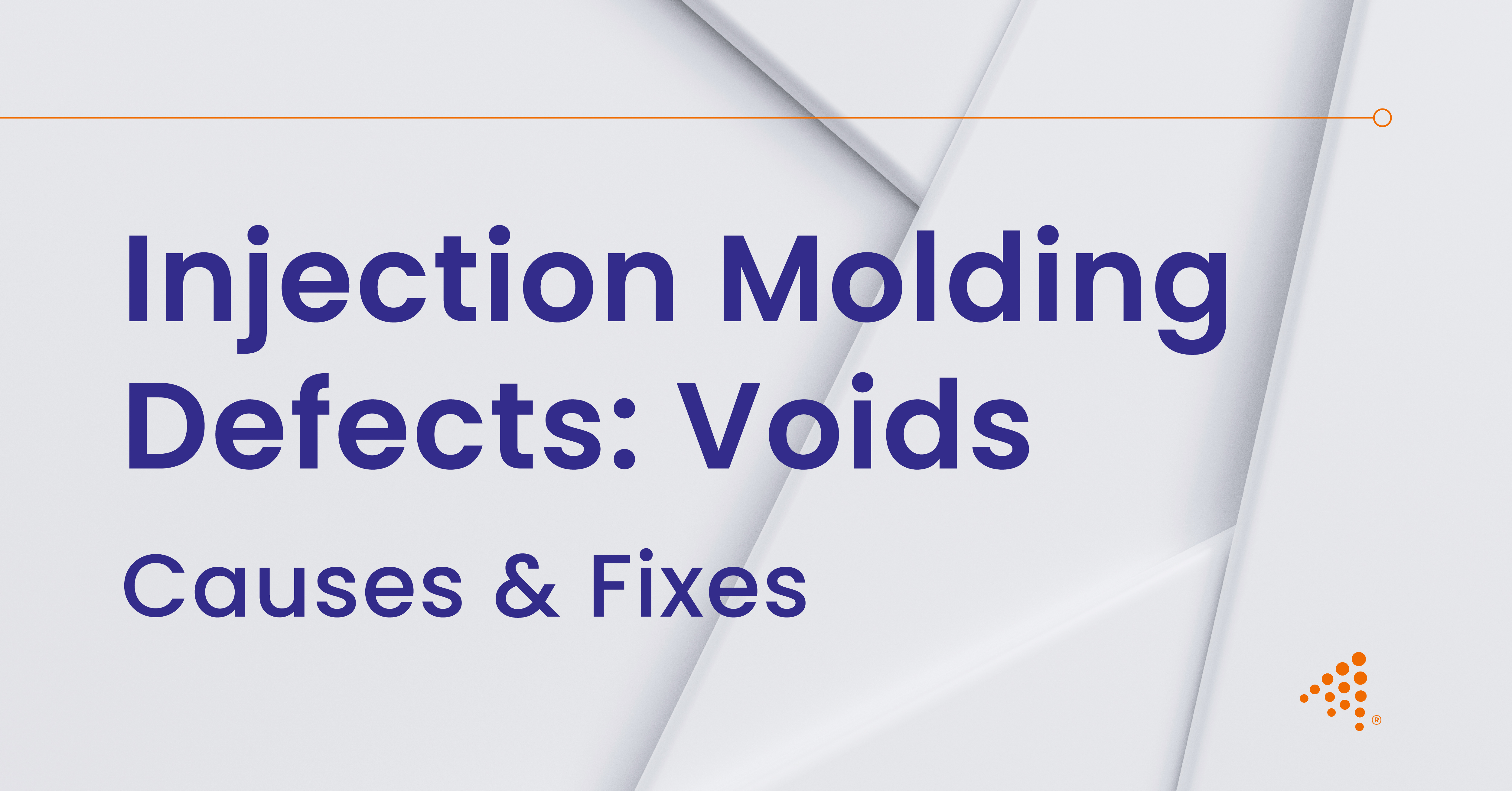
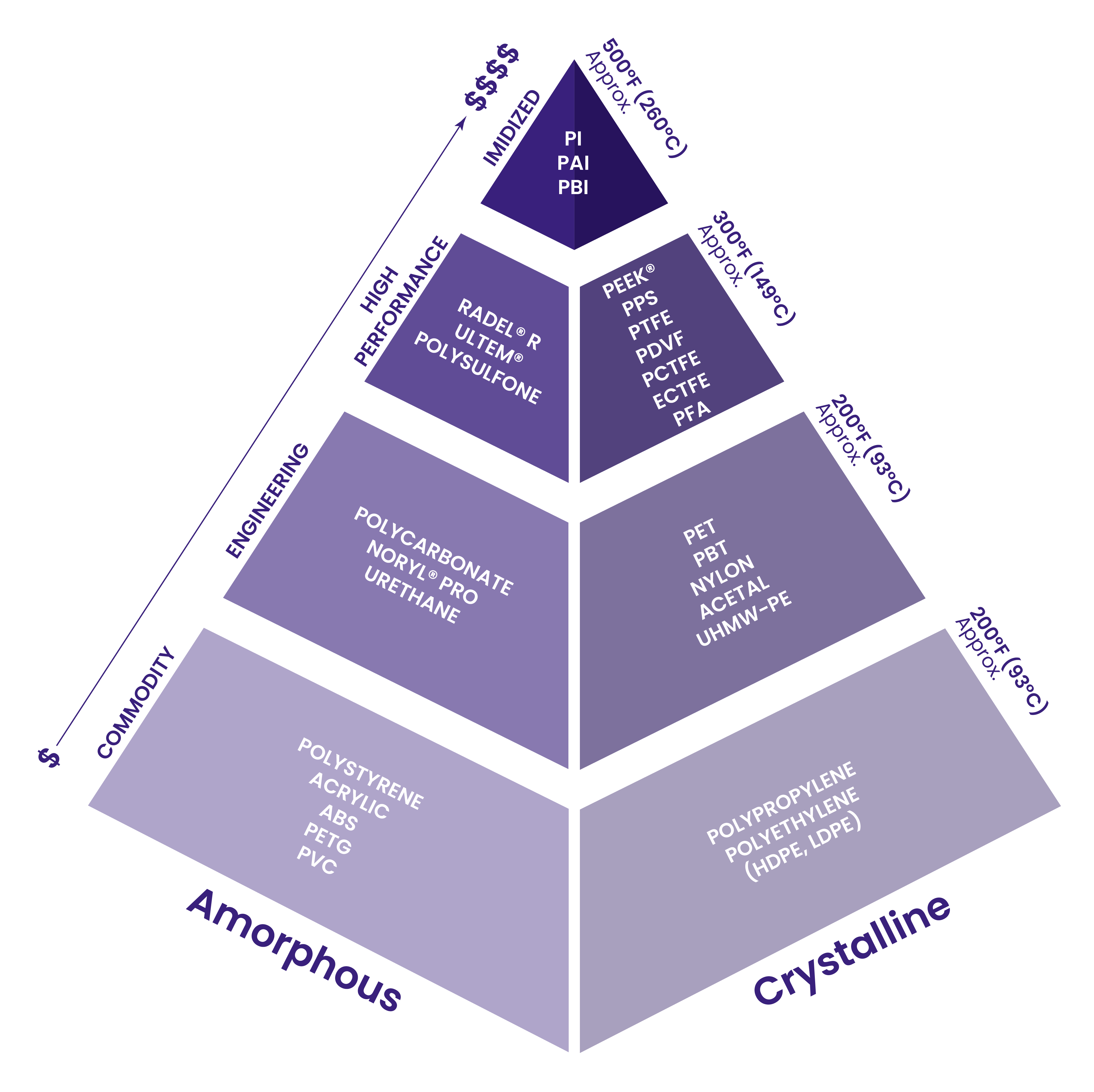
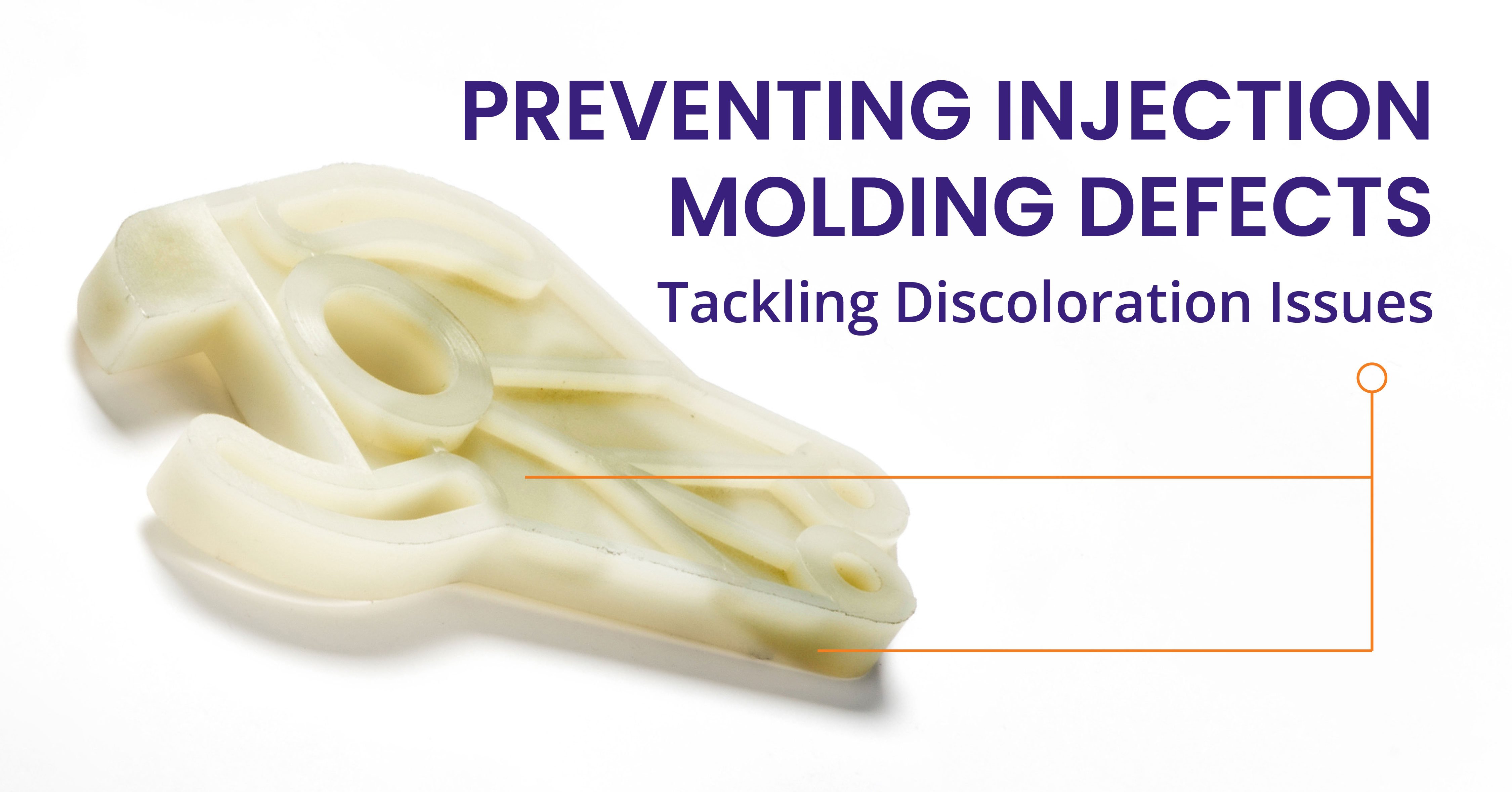
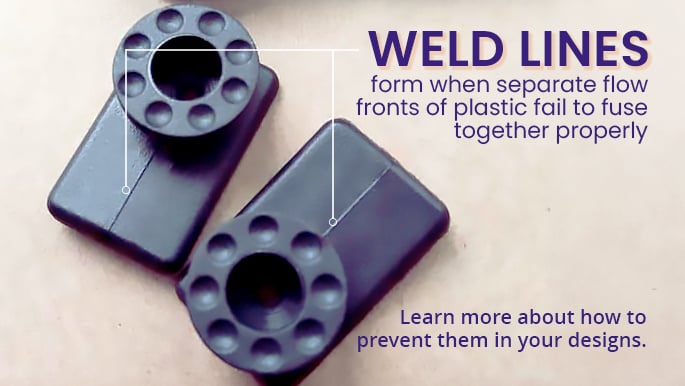
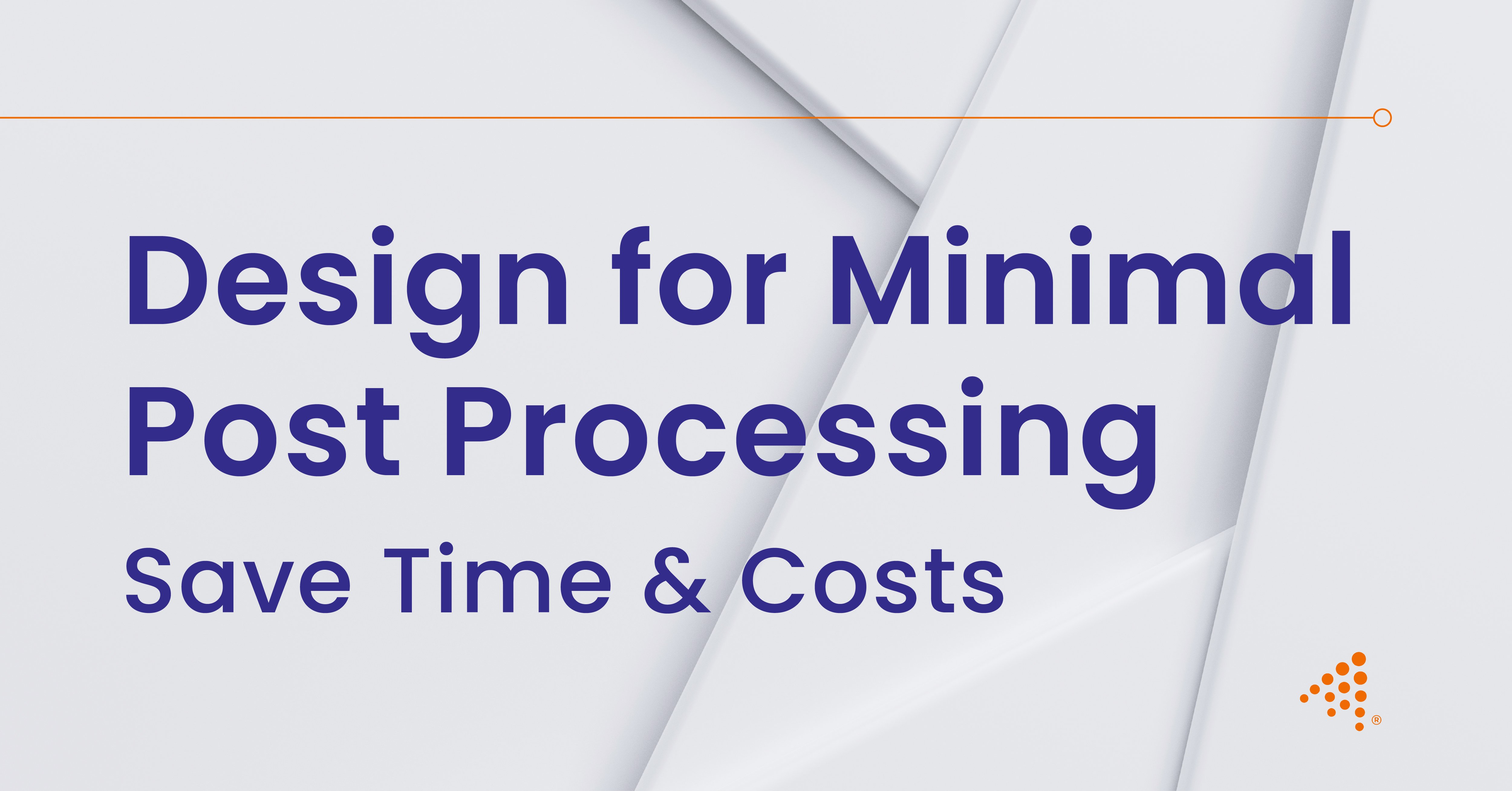
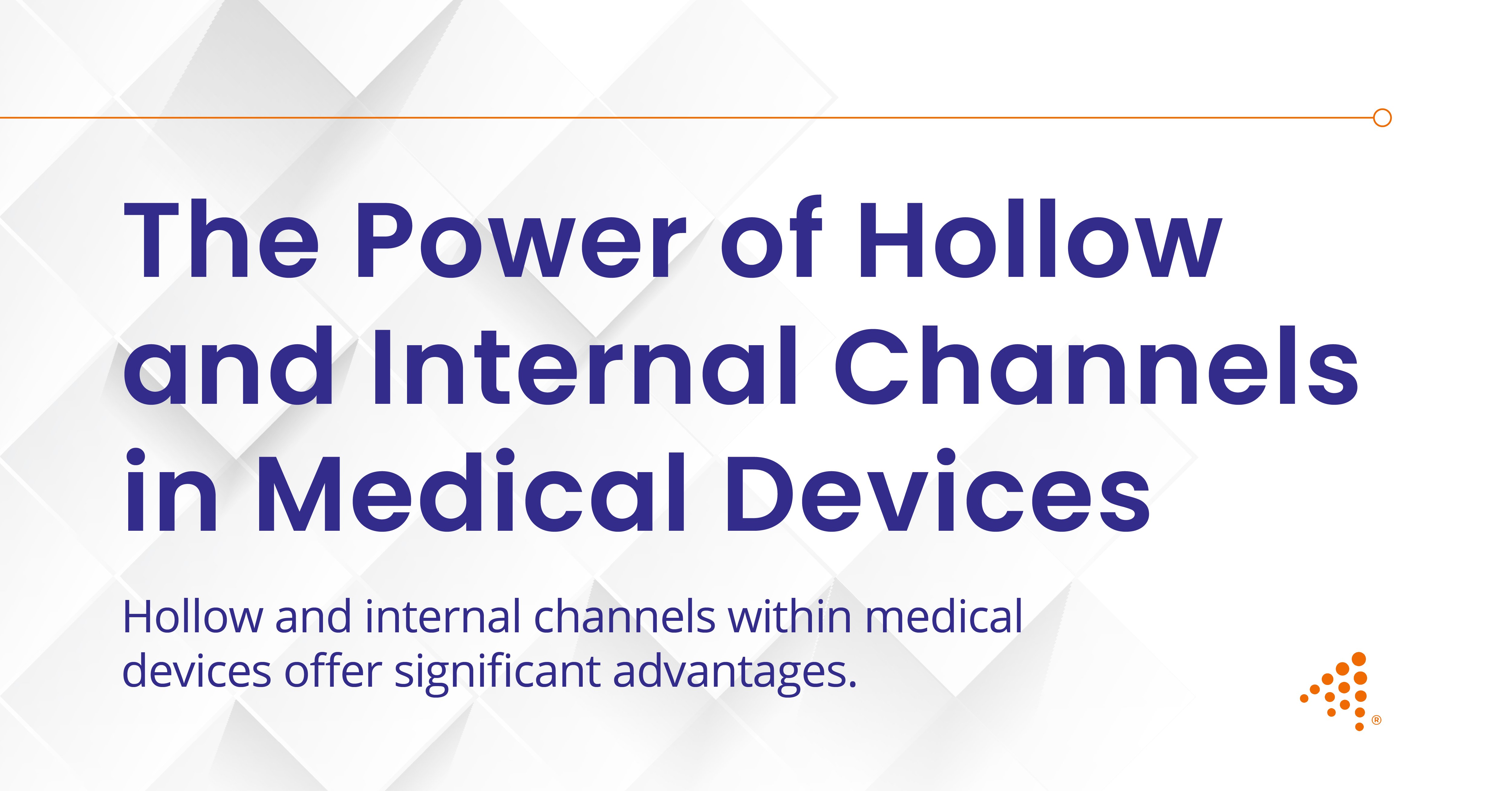
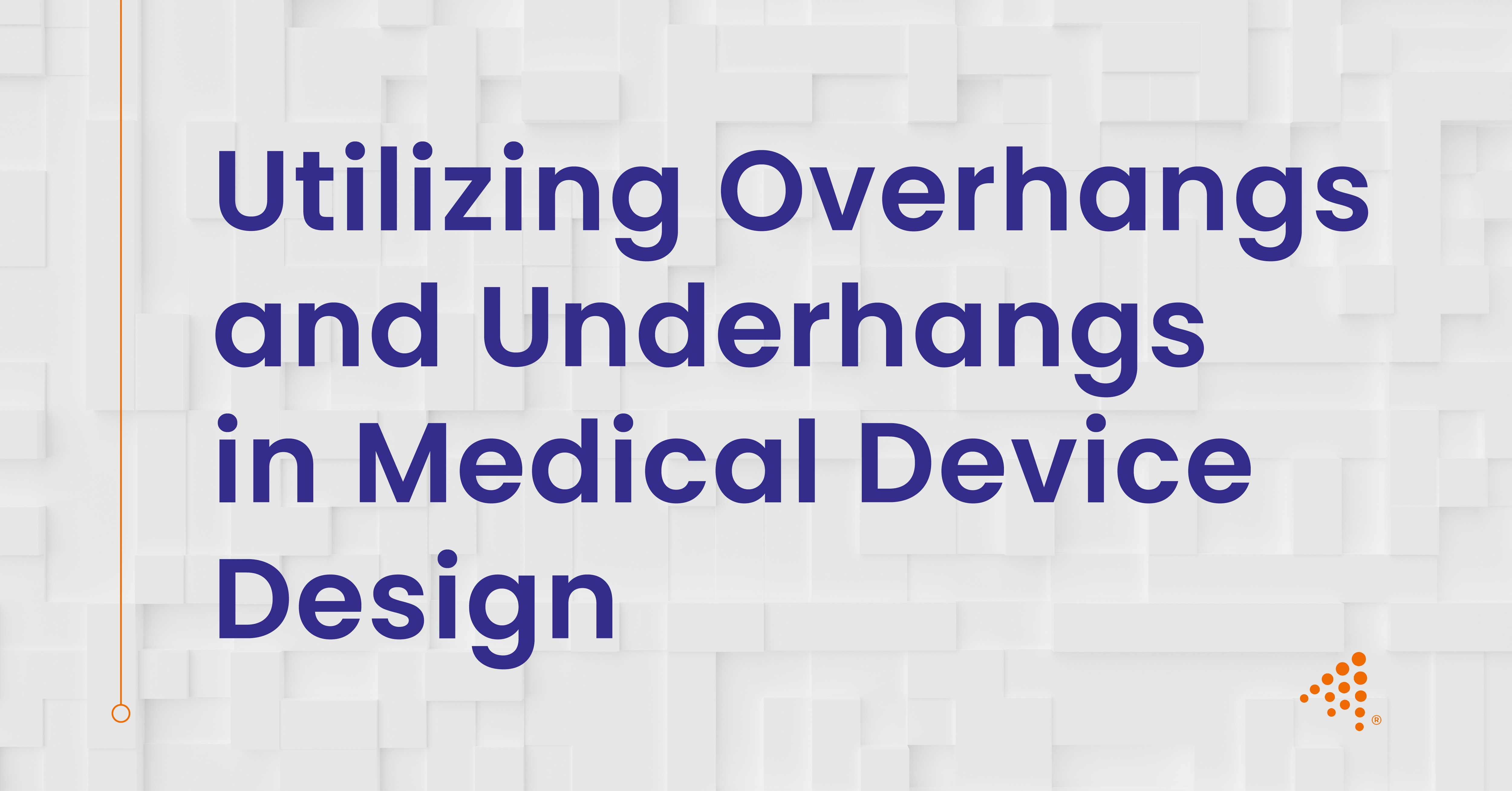
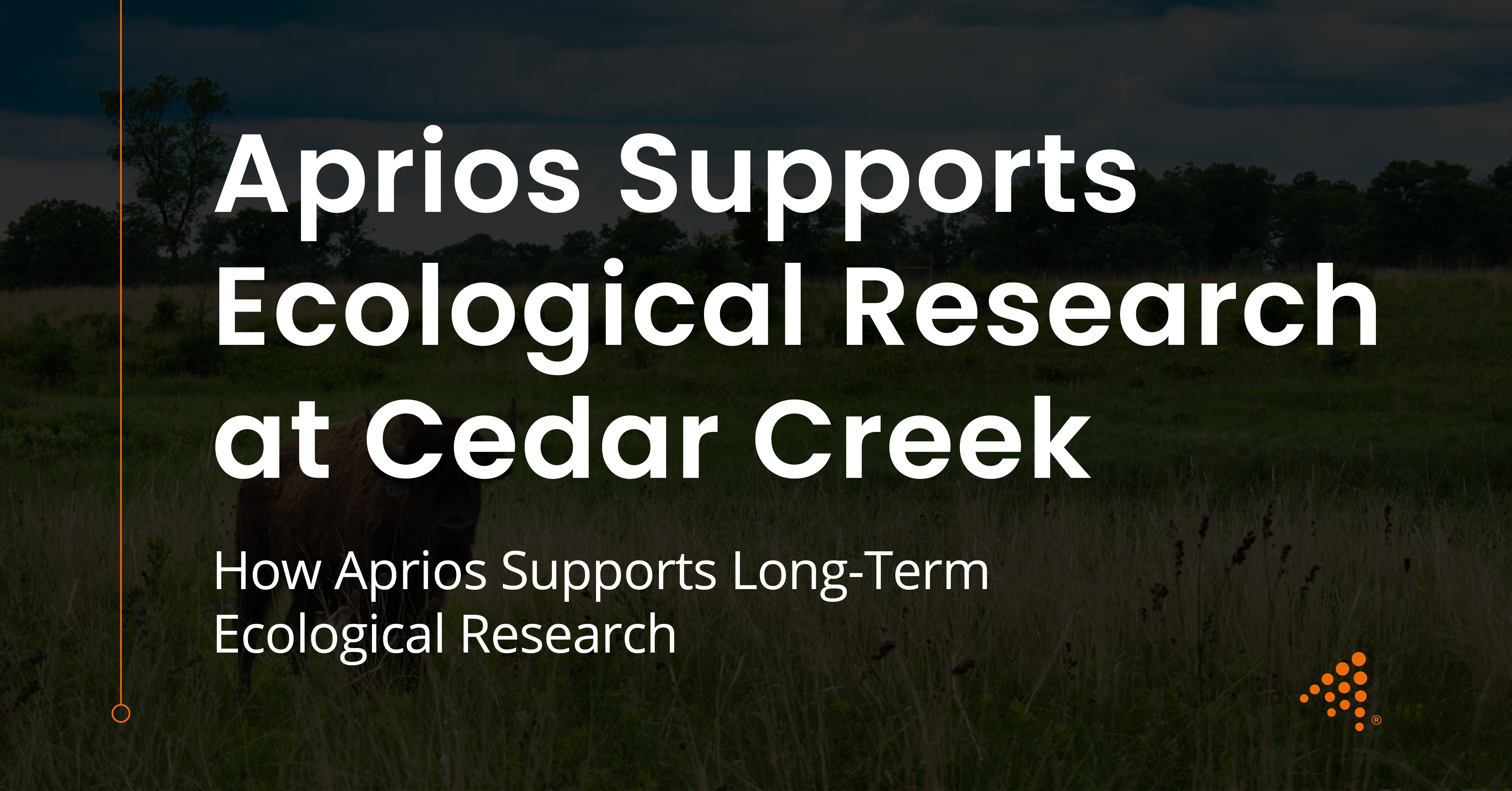
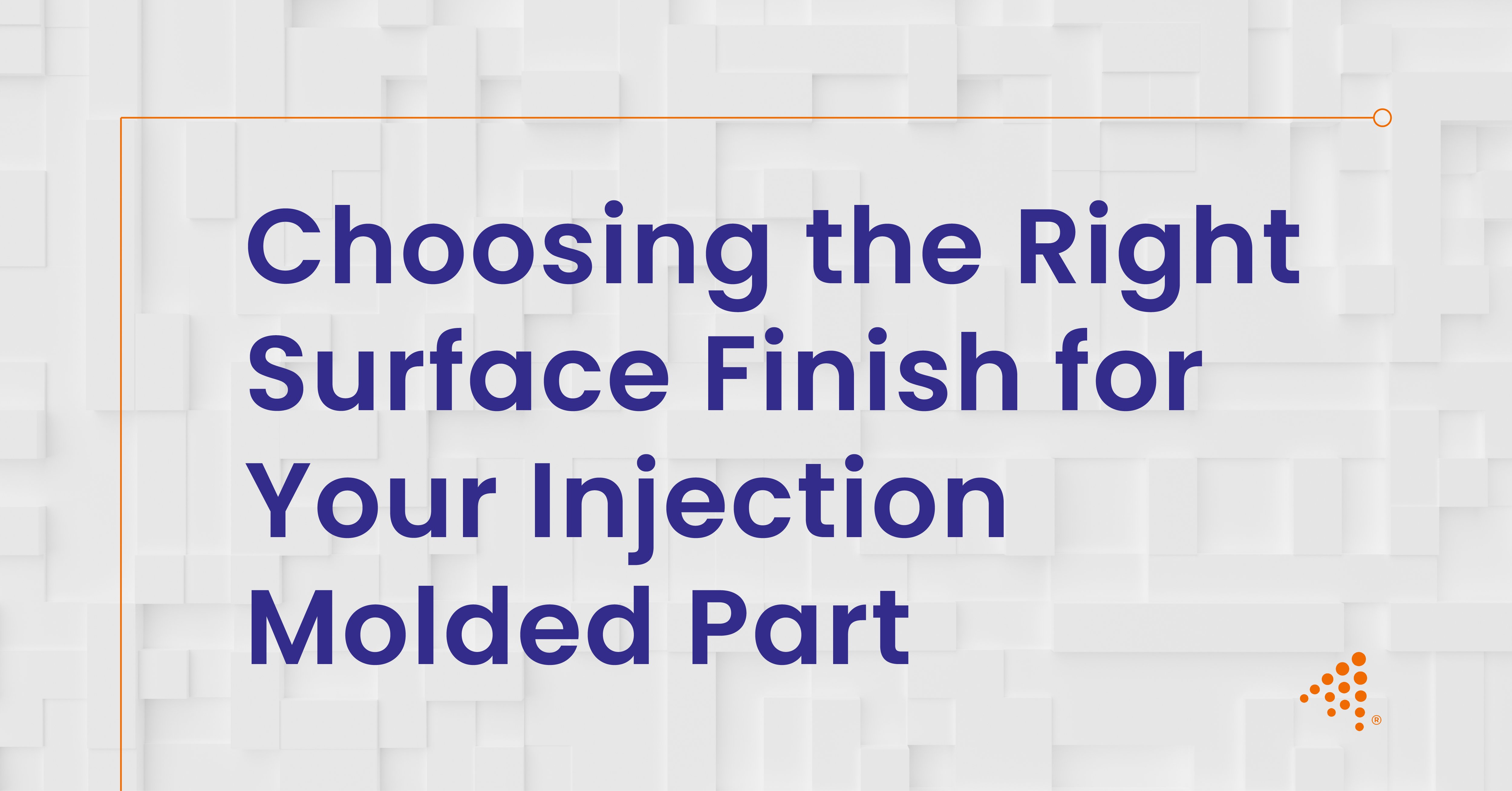
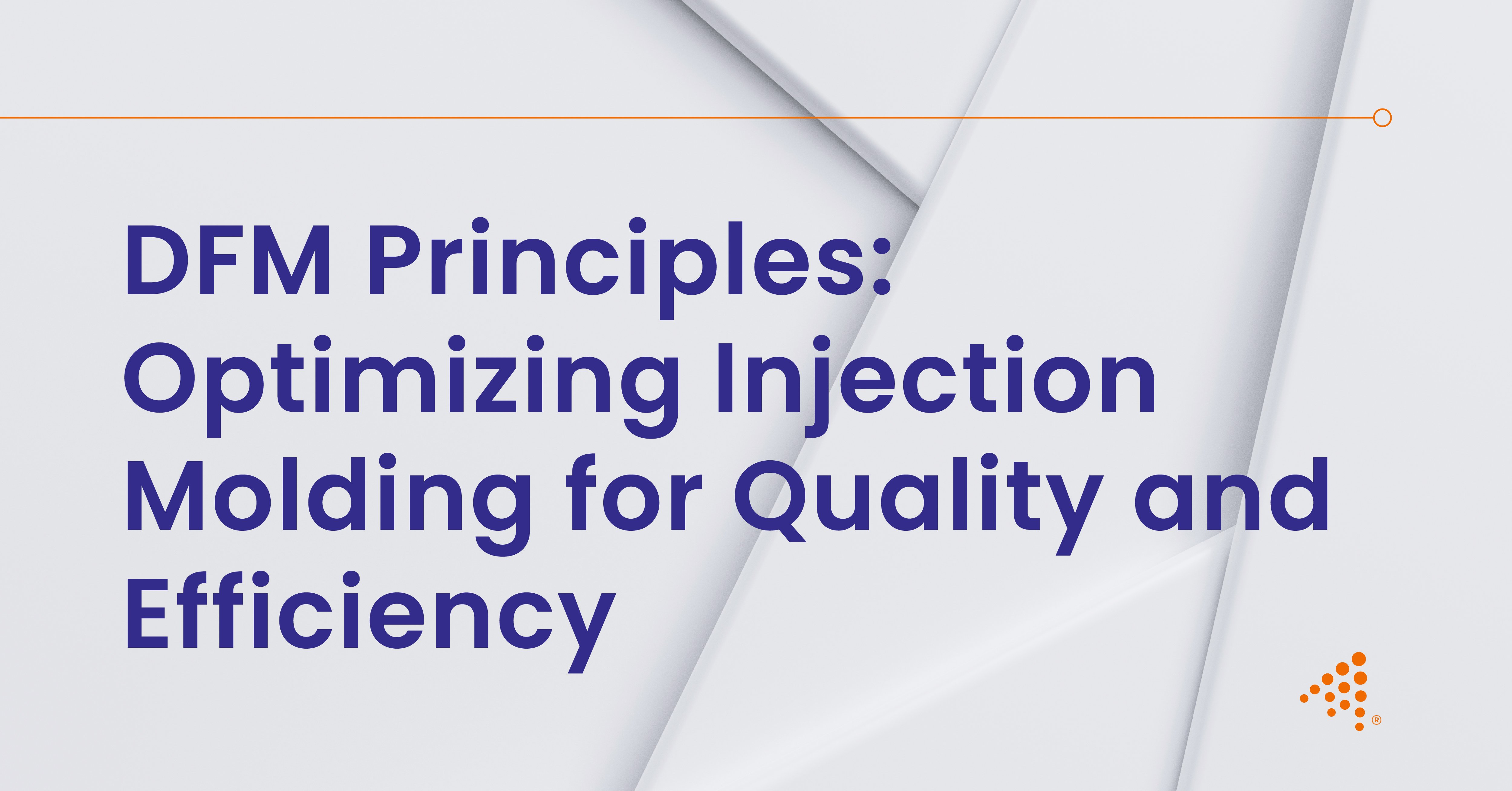
Make your designs production-ready with Aprios.