SECONDARY OPERATIONS
Hands-on partners,
every step of the way
From machining and bonding to assembly and finishing, our secondary operations ensure your products are completed to the highest standards.
What are Secondary Operations?
Secondary operations in injection molding refer to the additional processes performed on molded parts after the primary molding process to enhance their functionality, appearance, or assembly readiness. At Aprios, these operations encompass a variety of services, and we're constantly searching for new ways to serve our customers.
Design for Assembly (DFA)
Key DFA Considerations
Minimize the number of components to simplify assembly. For example, integrating multiple brackets and supports into a single molded piece reduces the number of parts that need to be assembled.
Design parts that are easy to handle and orient correctly. For instance, adding chamfered edges to parts ensures they are correctly aligned and easily placed during assembly.
Use standardized parts and fasteners to streamline the process. For example, using a single type of screw or bolt across the entire product reduces the need for multiple tools and simplifies the assembly process.
Create modular assemblies to facilitate easier and faster assembly. For example, designing sub-assemblies that can be pre-assembled separately and then easily snapped or bolted together during final assembly.
Incorporate self-locating features like dowel pins and corresponding holes to ensure perfect alignment during assembly. Error-proof your designs with keyed slots or tabs, allowing components to be assembled only in the correct orientation. From initial concept to final product, our secondary operations enhance the reliability and efficiency of your production process.
Choose appropriate fastening methods that are quick and reliable. For instance, using snap-fits or clips instead of screws to reduce assembly time and eliminate the need for additional tools.
What Our Secondary Operations Can Do for You
By incorporating secondary operations, supply chain managers and product engineers can achieve greater precision, improved product performance, and faster time-to-market. These services ensure that the molded components meet the exact specifications and quality standards required for your final product, optimizing the overall manufacturing process and reducing the need for external suppliers.
Bonding
We offer specialized bonding techniques to join plastic components, ensuring strong and durable connections. Our bonding processes are tailored to the specific materials and application requirements. This guarantees optimal performance and longevity for your products.
-
Spin WeldSpin welding is an effective method for joining thermoplastic parts using rotational friction. It produces a clean, strong bond without the need for additional adhesives or fasteners. This process is ideal for high-volume production and applications requiring reliable joints.
-
Ultra SonicUltrasonic welding uses high-frequency sound waves to bond plastic parts together. This process is quick, efficient, and produces high-strength joints without the need for additional materials. It is ideal for precision applications and high-volume production.
-
Thread Inserts
Thread inserts are used to create strong, wear-resistant threads in plastic components. We offer a variety of insert installation methods, including heat staking and ultrasonic insertion. These inserts enhance the durability and functionality of your assembled products.
-
Heat StakingHeat staking is a process where controlled heat and pressure are applied to deform plastic, creating a strong bond or mechanical joint. This technique is commonly used for inserting metal components into plastic parts. It provides a secure and permanent assembly solution.
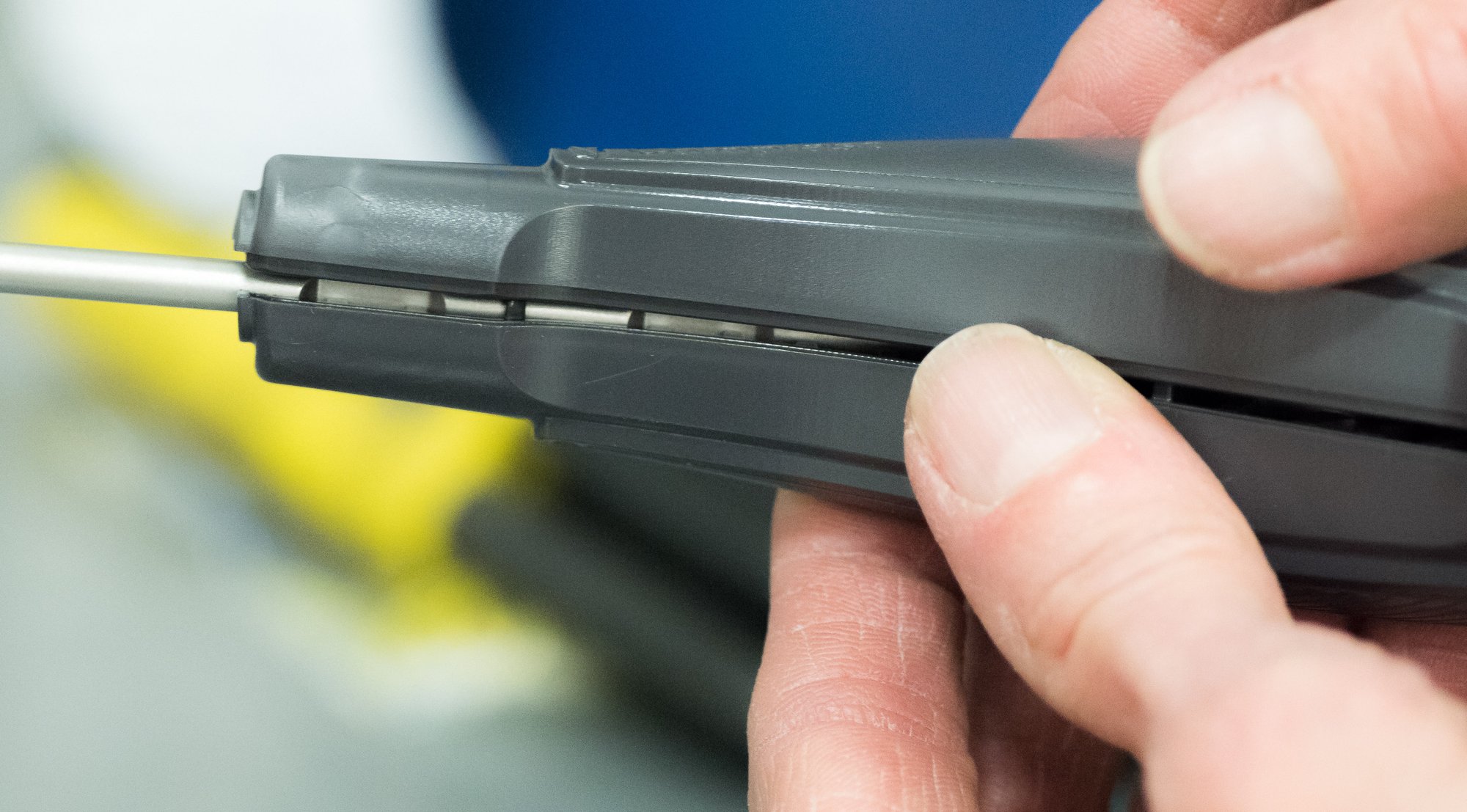
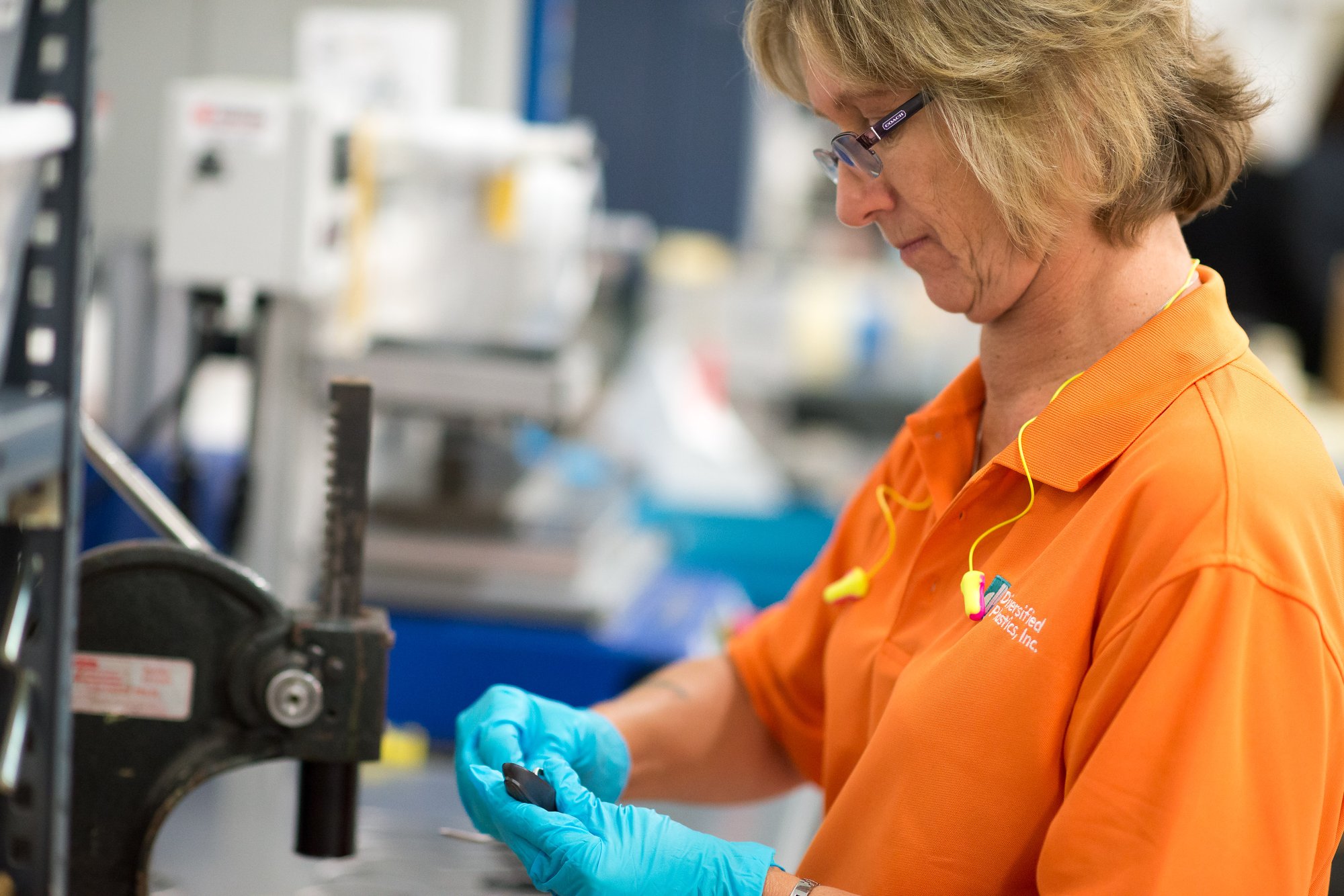
Machining
Our machining services, including drilling, tapping, and milling, ensure precise modifications to plastic components. We use advanced CNC machinery to achieve high accuracy and consistency. These services are essential for creating custom parts and meeting specific design requirements.
-
Drill Tap
Drill tap services create threaded holes in plastic components, enabling secure fastening. This process combines drilling and tapping in a single operation, improving efficiency. It is ideal for producing parts that require threaded inserts or fasteners.
-
Milling
Milling services involve the removal of material from plastic parts to achieve the desired shape and features. Our CNC milling capabilities ensure precise and consistent results. Milling is used for creating complex geometries and custom designs.
-
CNC Mill
CNC milling provides high-precision machining for plastic components. This automated process allows for complex shapes and fine details to be accurately produced. CNC milling ensures repeatability and high-quality finishes for all machined parts.
And a whole lot more including....
Our assembly line capabilities include the integration of various components into a final product. We manage everything from simple assemblies to complex multi-part constructions. This ensures efficient production and consistent quality across all assembled units.
Our clean room assembly services cater to industries requiring contamination-free environments. We provide assembly solutions for medical devices, electronics, and other sensitive products. This ensures high standards of cleanliness and product integrity.
Post-processing and finishing services enhance the appearance and functionality of molded parts. Techniques such as deburring, polishing, and painting are applied to achieve the desired final product quality. These processes ensure your products meet aesthetic and performance standards.
Our packaging services ensure that your finished products are protected and ready for transit or storage. By integrating packaging with our other secondary operations, we provide a seamless and efficient end-to-end solution, reducing the need for multiple suppliers.
Pad printing allows for precise and detailed application of graphics, logos, and text on plastic parts. This technique is ideal for branding, instructional labels, and decorative elements. It ensures high-quality, durable prints on a variety of surfaces.
Hot stamping applies metallic or colored foil to plastic parts for a decorative finish. This technique adds visual appeal and can be used for branding, labeling, or decorative purposes. It ensures a durable and high-quality imprint on the surface.
Medical wash services ensure that plastic components meet stringent cleanliness standards. This process removes contaminants and prepares parts for use in medical applications. Our clean room facilities and advanced washing techniques guarantee the highest levels of hygiene and safety.
Frequently Asked Questions
-
What types of post-processing services do you offer?
Our secondary operations include a wide range of post-processing services, such as machining, bonding, sonic welding, and assembly. These services ensure that your parts are finished to the highest standards and ready for immediate use.
-
Can you handle complex assemblies?
Yes, we specialize in handling complex assemblies, providing precise and reliable post-processing solutions that meet your specific requirements. Our experienced team ensures that each assembly is completed with meticulous attention to detail.
-
Do you offer packaging services for finished products?
Yes, we offer packaging services to protect your finished products during transit and storage. Our packaging processes adhere to strict cleanliness protocols, ensuring that your products remain secure and free from contamination.
-
What are the benefits of your secondary operations?
Our secondary operations add value to your products by providing high-quality post-processing services. This reduces the need for multiple suppliers, streamlines production, and ensures consistency and reliability in the final product.
Design for Assembly: A Guide for Engineers & Product Designers
Streamline your builds, reduce costs, and boost reliability—starting at the design stage.
WHAT'S INSIDE:
- Core DFA principles like part reduction, modularity, and fastener elimination
- How to design parts for easy, error-proof assembly
- Strategies for cost reduction and material efficiency
- Tips for sustainability, disassembly, and repair
- Common DFA mistakes and how to avoid them