TOOLING
Making reliability repeatable.
Precision tooling design, fabrication and repair.
Design, Create, Transfer, Repair
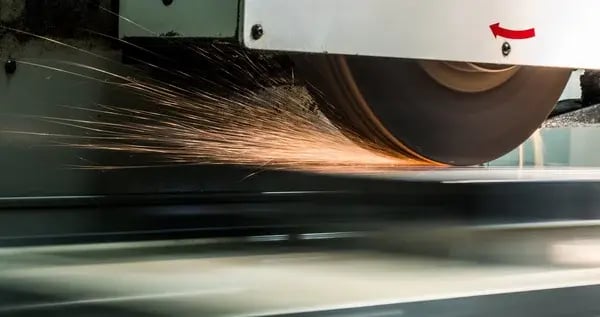
Our Tooling Capabilities
We’re proud to offer a broad range of tooling capabilities. With our focus on design and creation, we’re your team for prototyping, production, and more.
-
In-House Tool Design, Modification, and Repair: Doing everything in-house reduces costs and lead times.
-
Flexibility and cost-efficiency: Source domestically or offshore to best meet your manufacturing needs.
-
Tooling DFM (Design for Manufacturability): Lower costs with a simplified, optimized, and refined design process.
-
Tool Validation: Prevent defects and surprises with tool validation customized for you.
-
Tool Transfer Guidance: With expert support at every step of the process, Aprios aids you in the tool transfer process so you can get back to production.
Experts in Tool Design
Design for Manufacturing (DFM) in tooling focuses on optimizing the design of molds to enhance the efficiency and quality of the injection molding process. By considering factors such as ejection and cooling, gate placement, mold flow analysis, draft angles, and part consolidation, we ensure that the tooling is tailored to produce high-quality parts with minimal defects. Our DFM expertise helps in reducing cycle times, improving product durability, and minimizing production costs, ensuring an efficient manufacturing process.
-
Ejection and Cooling Considerations
Plan for Ejection: Ensure the design includes features that facilitate easy ejection, such as ejector pin locations. For example, flat surfaces for ejector pins to push against on the base of a complex component.
Efficient Cooling: Design parts to allow for effective cooling within the mold to reduce cycle times and improve quality. For example, designing a part with consistent wall thickness allows for uniform cooling.
-
Gate Placement
Optimize Gate Locations: Proper placement of gates ensures uniform filling and minimizes defects. For example, placing the gate at the thickest section of a part helps ensure proper flow and reduces the risk of sink marks in thin areas.
-
Mold Flow Analysis
Conduct Mold Flow Analysis: Use simulation software to predict the flow of molten plastic, identify potential issues like air traps, weld lines, or hotspots, and adjust the design accordingly. For example, simulating the injection molding process for a car dashboard can help optimize gate locations and cooling channels.
-
Draft Angles
Include Appropriate Draft: Adding a draft angle (typically 1-2 degrees) on the walls of the part allows it to be easily ejected from the mold. For instance, a plastic cup should have slight tapering walls to facilitate ejection.
-
Part Consolidation
Reduce Number of Parts: Where possible, consolidate multiple parts into a single molded piece to reduce assembly time and cost. For example, designing a single-piece snap-fit housing for a small electronic device instead of multiple interlocking parts.
Tooling Matrix
Is quick turn tooling right for your project? Contact our experts to learn more.
.png?width=2000&height=1266&name=Quick%20Turn%20Tooling%20Comparison%20Transparent%20(1).png)
Molds tailored to your needs.
We assist you in selecting the optimal mold for your project.

Elite Performance Molds (Class 101)
- Production: High-volume
- Max Cycles: 1,000,000+
- Materials: Superior grade
- Construction: Stainless steel base
- Price: $$$$$

Premium Production Molds (Class 102)
- Production: Medium to high
- Max Cycles: 1,000,000
- Materials: Premium
- Ejection: Guided, wear plates
- Price: $$$$

Standard Production Molds (Class 103)
- Production: Medium-volume
- Max Cycles: 500,000
- Materials: High-grade
- Design: Detailed
- Price: $$$

Economy Production Molds (Class 104)
- Production: Low-volume
- Max Cycles: 100,000
- Materials: Mild steel, aluminum
- Cooling: In cavities, cores
- Price: $$

Precision Prototype Molds (Class 105)
- Prototypes Ideal
- Max Cycles: 500
- Materials: Various (aluminum, cast metal)
- Cooling: Basic
- Price: $
.png?width=750&height=750&name=Supply%20chain%20IMGs%20(6).png)
Flexibility and Customization
Aprios delivers tooling that meets your specific needs - both onshore and offshore manufacturing.
We adapt everything we do to your project’s specific constraints, delivering the right solutions every time.
Our team is with you every step of the way- through tool transfers and DFM.
Tooling Design, Creation, and Repair
-
What types of tooling services do you offer?
We offer comprehensive tooling services, including design, creation, and repair. Our team can develop new tools, modify existing ones, and perform repairs to ensure optimal performance and longevity.
-
How do you ensure the quality of your tooling?
Our tooling services adhere to rigorous quality control standards. We leverage design software, mold-flow analysis, precision machining, and thorough measurement to ensure that each tool is performing optimally.
-
Can you transfer and modify tools from other manufacturers?
Yes, we have a defined project management process for intaking tools from other manufacturers. We can repair and modify these tools to meet your specific production needs and get your production back on track quickly.
-
What is the typical lead time for creating new tooling?
The lead time for creating new tooling varies based on complexity and requirements, but our quick-turn tooling services can deliver parts within a month after placing an order.
-
Do you offer maintenance services for existing tools?
Yes, we provide maintenance and repair services for existing tools to ensure they remain in optimal condition and continue to produce high-quality parts.
Let's talk about tooling
From prototyping to tool transfer to onshore and offshore manufacturing. Our experts make the process quick and easy from start to finish.
1 min read
Streamlining Prototyping: The Benefits of Quick Turn Tooling
Jan 24, 2025 by Nick Erickson
3 min read
Key Red Flags to Watch for When Choosing an Injection Molder
Jul 3, 2025 by Nick Erickson